Hey there,
It’s Mikal Khoso and welcome to Trajectory, a newsletter about where the world is heading, delivered straight to your inbox.
The High-Level This Week: The world is in the early days of a fourth industrial revolution. This revolution will connect the global manufacturing sector to the internet, further automate production but most importantly enable us to produce in a way that has never been possible before — mass personalization.
To learn more, read on.
If you haven’t already, subscribe here. If you liked this week’s edition and think someone else you know would find it interesting please take a couple seconds to share it via email or on social media.
Intellectual Sparks
Humans are cooling down so average body temperature is no longer 37°C: A fascinating example of the impact of civilization on our biology
The Middle Eastern Problem Soleimani Figured Out: Soleimani single-handedly reshaped the political architecture of the Middle East by recognizing this one simple thing
I Don't Need Your Civil War: What is the general structure of a civil war?
Putin’s Pick for Prime Minister Is a Bureaucratic Superman: President Putin is reshaping the Russian government in a profound way.
The Hidden Dangers of the Great Index Fund Takeover: Blackrock, Vanguard and State Street’s power is only growing.
Key Issue: The Future of Manufacturing
The rumors of the demise of American manufacturing have been greatly exaggerated. In fact, American manufacturing is experiencing something of a renaissance. In 2018, the United States added 261,000 jobs in the manufacturing sector, mirroring an increase of 207,000 in 2017. This job growth has primarily been powered by small, high-technology firms working with cutting-edge manufacturing capabilities. Today, manufacturing stands on the precipice of a profound transformation that many are calling Industry 4.0, or the “fourth industrial revolution.”
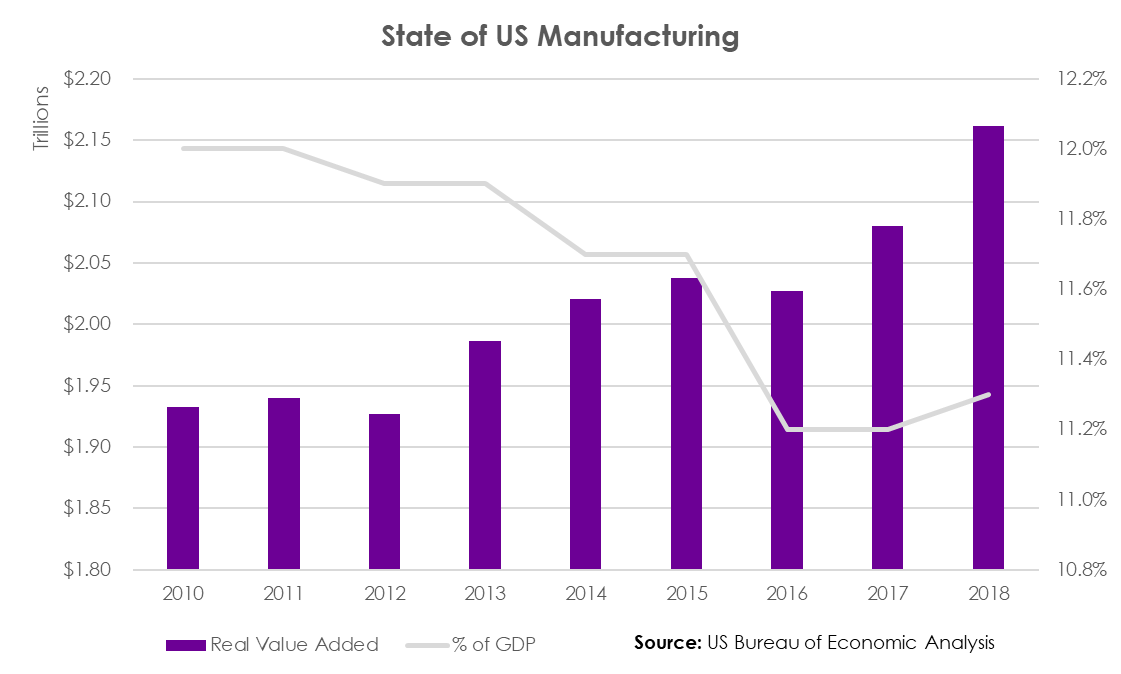
The First Three Industrial Revolutions
The first Industrial Revolution marked a profound shift in human history and transformed the entire endeavour of human civilization radically. The 19th century was marked by a shift from an agrarian-centric economy to a manufacturing and production-centric economy. This revolution was powered primarily by coal, water and steam energy. The Watt Steam engine and its successors enabled production and productivity to soar and enabled the rapid industrialization seen in Europe in the century to follow. In 1800, the United Kingdom had 30,000 steam horsepower in installed capacity. By 1870 this had soared to 1.7m in steam horsepower in installed capacity.
The second industrial revolution was set off in the early 20th century almost single handedly by the Ford Motor Company. The second industrial revolution saw electricity become the primary source of power in production as opposed to steam or water-powered systems. In addition, industrial production rapidly professionalized and adopted new frameworks during this revolution. Ford pioneered the “assembly line” which quickly became the primary method of industrial production globally. The assembly line was a revolution in production methodologies and allowed Ford Motor Company to reduce the time necessary to assemble a Model T chassis from 12.5 hours to just 1. Similar advancements were developed by the Japanese industrial base after WWII, specifically by Toyota Motor Company, including just-in-time manufacturing, lean manufacturing and the “kaizen” method. These new methodologies launched an era of mass production globally. The efficiency and productivity of industrial organizations increased by orders of magnitude globally, unleashing a century of tremendous and unparalleled economic growth.
By the 1970s and 1980s, at the start of the third industrial revolution, industrial production remained highly concentrated in the United States, Western Europe and Japan. During this time, automation and digitization of manufacturing were first introduced. The application of robotics to assembly and manufacturing lines rapidly increased speed, precision and productivity to levels never seen before, all while reducing overall labor costs. Since 1970 the United States has lost over 6 million manufacturing jobs despite a steady increase in industrial production. The third industrial revolution was also marked by the first digitization efforts in the industry. The first-generation of product lifecycle management (PLM), manufacturing execution systems (MES) and supervisory control and data acquisition (SCADA) systems were developed and implemented worldwide. Companies like PTC, IBM and Plex developed solutions that dominate manufacturing to this day.
The Fourth Industrial Revolution:
Sensors, Machine Learning and 3D Printers
Today, the world is at the beginning of multi-faceted transformation of manufacturing - the fourth industrial revolution. The fourth industrial revolution will start where the third industrial revolution left off - the digitization of manufacturing. The fourth industrial revolution ushers in the application of sensors, machine learning, data, cloud-first software and additive manufacturing to the production process.
The application of sensors to every machine and stage in the manufacturing process will create huge streams of real-time data on production. Combined with machine learning, this web of sensors - the so called “internet of things” - will allow for even further streamlining of manufacturing. Similarly, cloud-native software will enable factories to be more responsive to demand and unlock the possibility of truly “networked manufacturing” - interconnected factories working collaboratively to produce final goods. Finally, additive manufacturing promises to be the most exciting technology gaining momentum in the fourth industrial revolution.
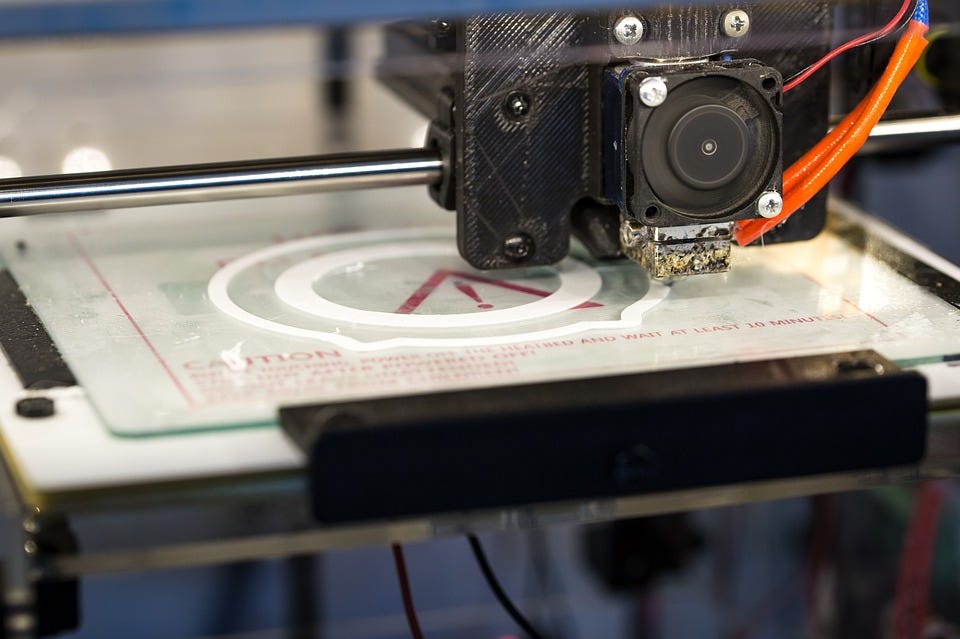
Additive manufacturing involves the application of 3D printing technologies to the creation of parts, products and goods. Additive manufacturing is the fullest realization of digitized manufacturing. 3D printers take computer-aided design (CAD) files stored in computer harddrives and transform them into 3D objects made of metal, plastic, carbon fiber and more. Today, manufacturers can design a file in software, send it to a 3D printer and initiate the manufacturing of that part all in the cloud, in real time. Companies like Desktop Metal, Relativity Space, Makerbot, Fortify, Icon and many others are pioneering 3D printing across different manufacturing sub-sectors.
Additive manufacturing will unlock the most important paradigm shift in manufacturing since the rise of the assembly line - personalization. While the assembly line enabled the rise of mass production - hyperscale production of the same item millions of times over - the 3D printer will enable the rise of mass personalization. 3D printers will allow us to produce thousands and even millions of items each personalized to the needs and demands of each individual customer.
Our evolution as a civilization over the last two centuries has been closely tied to these various industrial revolutions. However, manufacturing has been slow to adapt to the opportunities of the internet era, but in the last few years a range of new technologies have begun to gain traction and the manufacturing industry is poised for large scale technological disruption. Manufacturing is going to become more digitized, more streamlined and more efficient in the decades to come. But most importantly the coming era of mass personalization in manufacturing will be a welcome antidote to the decades of mass-manufactured uniformity in consumer and commercial goods that we have all had no choice but to live with.